Case Study
QCD: Operational Excellence in Cold Chain Distribution
Established in 2006 as a division of Golden State Foods (GSF), Quality Custom Distribution (QCD) completes more than 35,000 refrigerated transport deliveries a week from 25 distribution centers strategically located throughout the United States. QCD leverages more than five decades of GSF distribution expertise, providing high-quality, custom distribution services at a competitive price.
Trusted by top industry brands, including Starbucks, Chipotle and Chick-fil-A, the company services nearly 7,500 restaurants nationally – totaling more than 1.8 million deliveries per year. QCD has a longstanding commitment to innovation and incorporates state-of-the-art technology in every aspect of its operations – from warehouse management systems to its single-platform fleet monitoring solution.
A Partnership Driving the Evolution of Cold Chain Monitoring
In 2012, QCD selected Coretex – which was acquired by EROAD in 2021 – to replace the costly and unreliable process of manual temperature monitoring of its reefer trailers. QCD has since deployed EROAD’s reefer fleet management solution in its entire trailer fleet, allowing the automated, continuous monitoring of air temperature from warehouse to restaurant.
A Fresh Approach to Continuous Temperature Monitoring
Throughout this ongoing partnership, EROAD has developed advanced functionality to align with QCD’s reputation for technological innovation and the capability to address customer requirements that go well beyond industry norms. Along the way, EROAD has advanced its capabilities for remote reefer control, two-way communication, hours of service compliance, geofencing and a host of management applications.
QCD was also instrumental in piloting CoreTemp: a simulated product temperature monitoring technology that uses artificial intelligence and advanced predictive analytics to eliminate the need for manual temperature checks. CoreTemp gives carriers and shippers real-time visibility into every moment of a trip, helping to ensure regulatory compliance, protecting perishable cargo and eliminating the risk of human error or intentional falsification associated with manual temperature checks.
Partnering with EROAD and implementing CoreTemp has helped QCD stand out among its competitors, even allowing it to set the standards to which other carriers are held, says Tim Bates, corporate quality systems director at QCD.
“The work we’ve done has cascaded into requirements for all of our competitors. So, our competitors have to comply with what we developed,” he says. “We want to continue to lead the charge and be on the cutting edge, because if you’re following you’re going to have to comply with someone else’s rules.”
The Results
Together, QCD and EROAD determined the precise specifications to ensure freshness for a variety of perishable food categories (dairy, refrigerated sandwiches, frozen food, etc.) and variable packing data sets (plastic-wrapped, cardboard boxes, pallet, etc.).
“The algorithm works flawlessly,” says Larkin Williams, senior director, QCD Western Region. “Everyone wants to make sure they know that the core temperature of their products is compliant. Being able to build on air temperature reading by receiving actual product temperature will allow us to communicate to our customer that they are receiving the highest quality of product every time.”
CoreTemp provides real-time compliance to QCD and its customers. The software-as-a-solution features on-demand, aggregated compliance views with live route progress and product temperature simulations. Moreover, the elimination of manual temperature checks has resulted in significant cost savings for QCD, Bates says.
“If you’re paying a driver hourly and it takes a few minutes for them to get valid temperature readings at each stop, it’s going to cost you in labor. Then this manual data needs to get input later by a supervisor and that’s going to cost money,” Bates says, adding that CoreTemp eliminates the expenses associated with manual temperature checks by automatically measuring and delivering temperature data.
CoreTemp also helps QCD and its customers ensure quality and reduce waste, per Bates.
“You can use it to show that you’re delivering higher quality product to the customer,” he says. “For instance, lettuce that is kept at 39 degrees will only last half as long as lettuce that’s kept at 34 degrees. That’s a big thing: If a restaurant can get their produce delivered closer to 34 degrees, they’re going to get better performance.”
Following the successful pilot program, QCD implemented the EROAD solution for all of its delivery routes.
“I think CoreTemp has helped elevate our game,” Bates says. “We’ve got a lot of powerful information that we never had in years past.”
Click here to learn more about CoreTemp
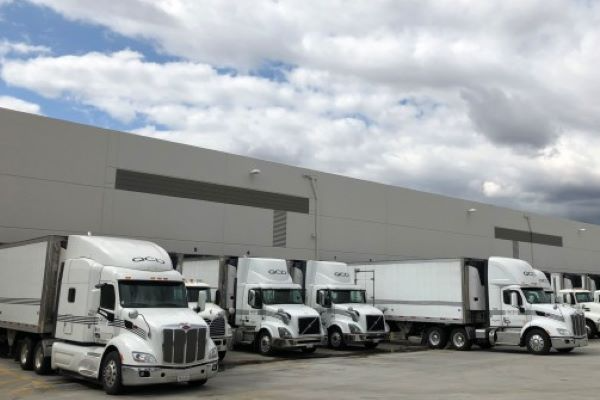
“I think CoreTemp has helped elevate our game. We’ve got a lot of powerful information that we never had in years past.”
Tim Bates
Corporate Quality Systems Director
Quality Custom Delivery
About Quality Custom Distribution
QCD is a leader in the quick service restaurant freight industry. In 2012, QCD chose Coretex – which was acquired by EROAD in 2021 – as its reefer telematics partner and continues to collaborate with EROAD, leveraging its deep expertise in reefer telematics and raw data to develop the future of cold chain solutions for its customers.